Case Study: Continuous Improvement Success in an Ottawa Manufacturing Firm
Ta
Introduction
In today's competitive market, continuous improvement is a crucial strategy for manufacturing firms aiming to enhance efficiency and maintain a competitive edge. This case study highlights the remarkable success of an Ottawa-based manufacturing firm that embraced continuous improvement methodologies to transform its operations and achieve outstanding results.
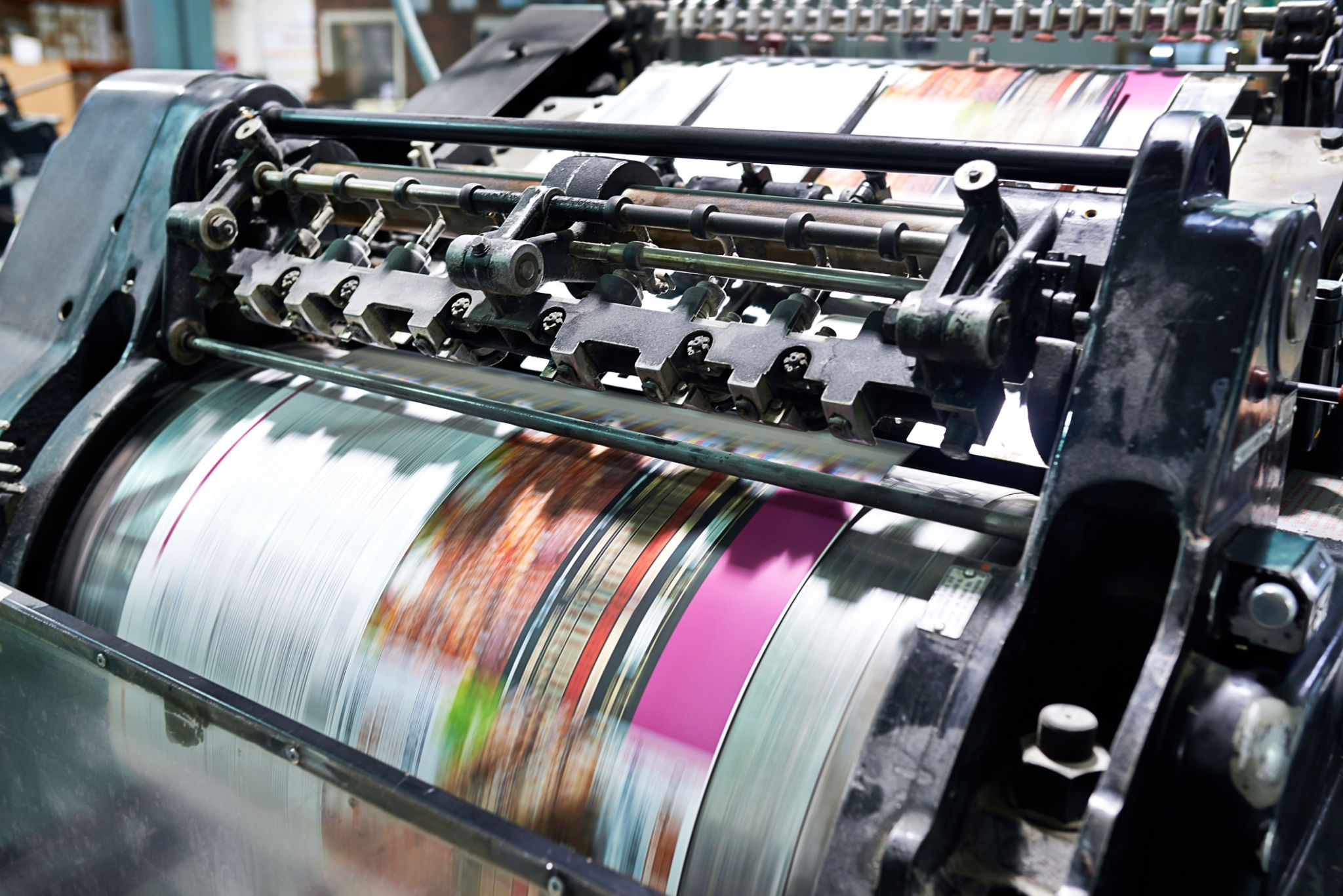
The Challenge
The Ottawa manufacturing firm faced several challenges that were impacting its productivity and profitability. These included outdated processes, high defect rates, and inefficient resource utilization. Recognizing the need for change, the management team decided to implement a continuous improvement strategy to address these issues and foster a culture of innovation.
Initial Assessment
The first step in their continuous improvement journey was a comprehensive assessment of their current processes. This involved gathering data, analyzing workflows, and identifying bottlenecks. The assessment revealed several areas where improvements could be made, such as reducing waste, optimizing production schedules, and enhancing quality control measures.
Strategy Implementation
With a clear understanding of the challenges, the firm developed a strategic plan to implement continuous improvement initiatives. This plan focused on three main areas:
- Adopting Lean Manufacturing principles to minimize waste and streamline processes.
- Implementing Six Sigma techniques to improve quality and reduce defects.
- Investing in employee training to empower staff with the skills needed to drive change.
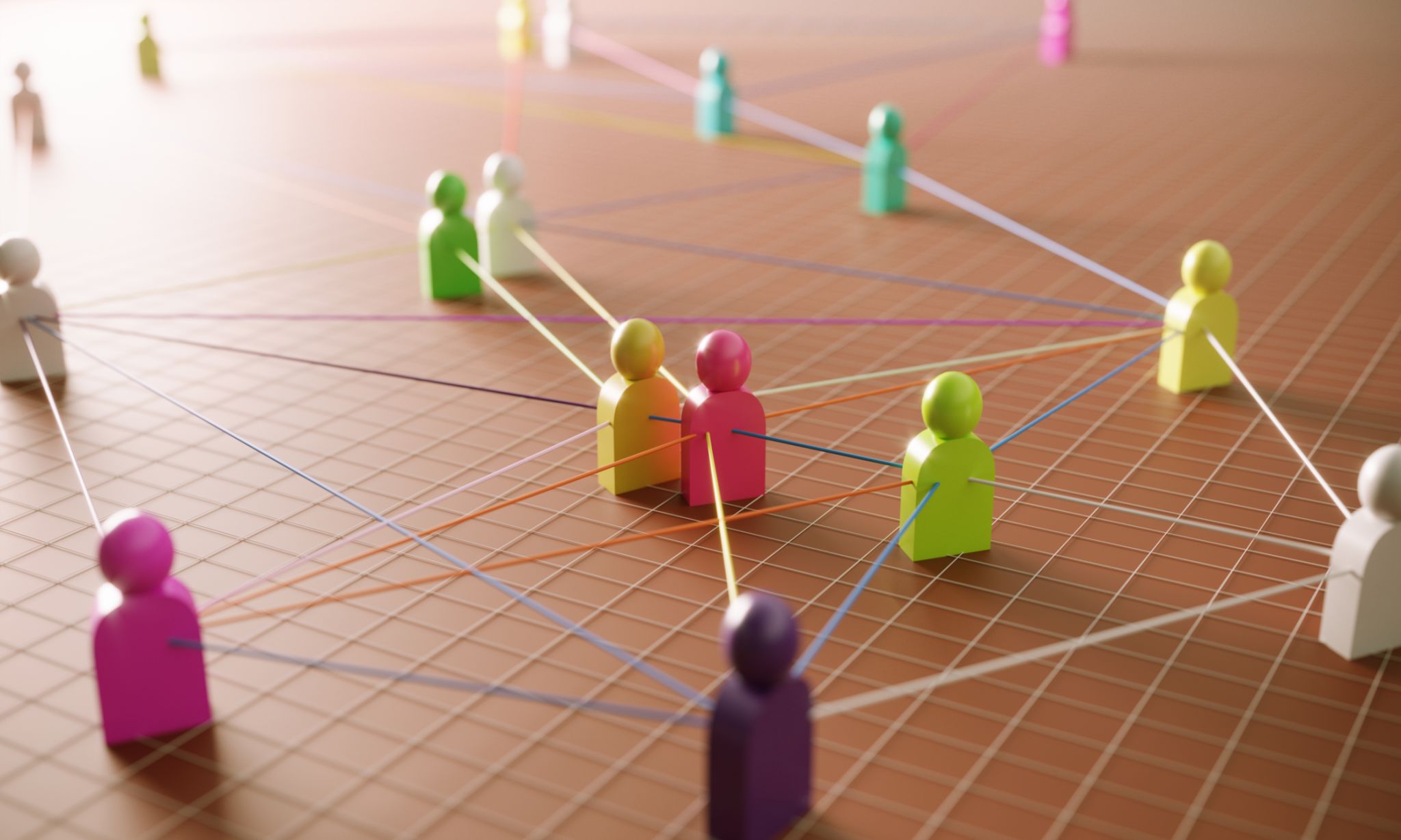
Lean Manufacturing
By adopting Lean Manufacturing principles, the firm was able to significantly reduce waste and improve efficiency. This involved revising workflows, eliminating non-value-added activities, and promoting a culture of continuous improvement among employees. As a result, production times were shortened, and costs were reduced.
Results and Benefits
The implementation of continuous improvement strategies yielded impressive results for the Ottawa manufacturing firm. Key benefits included:
- Reduced Defect Rates: By applying Six Sigma techniques, the firm saw a noticeable decrease in defects, leading to higher product quality and customer satisfaction.
- Increased Productivity: Streamlined processes and optimized resource utilization contributed to a significant boost in productivity.
- Cost Savings: The reduction in waste and improved efficiency led to substantial cost savings, positively impacting the firm's bottom line.
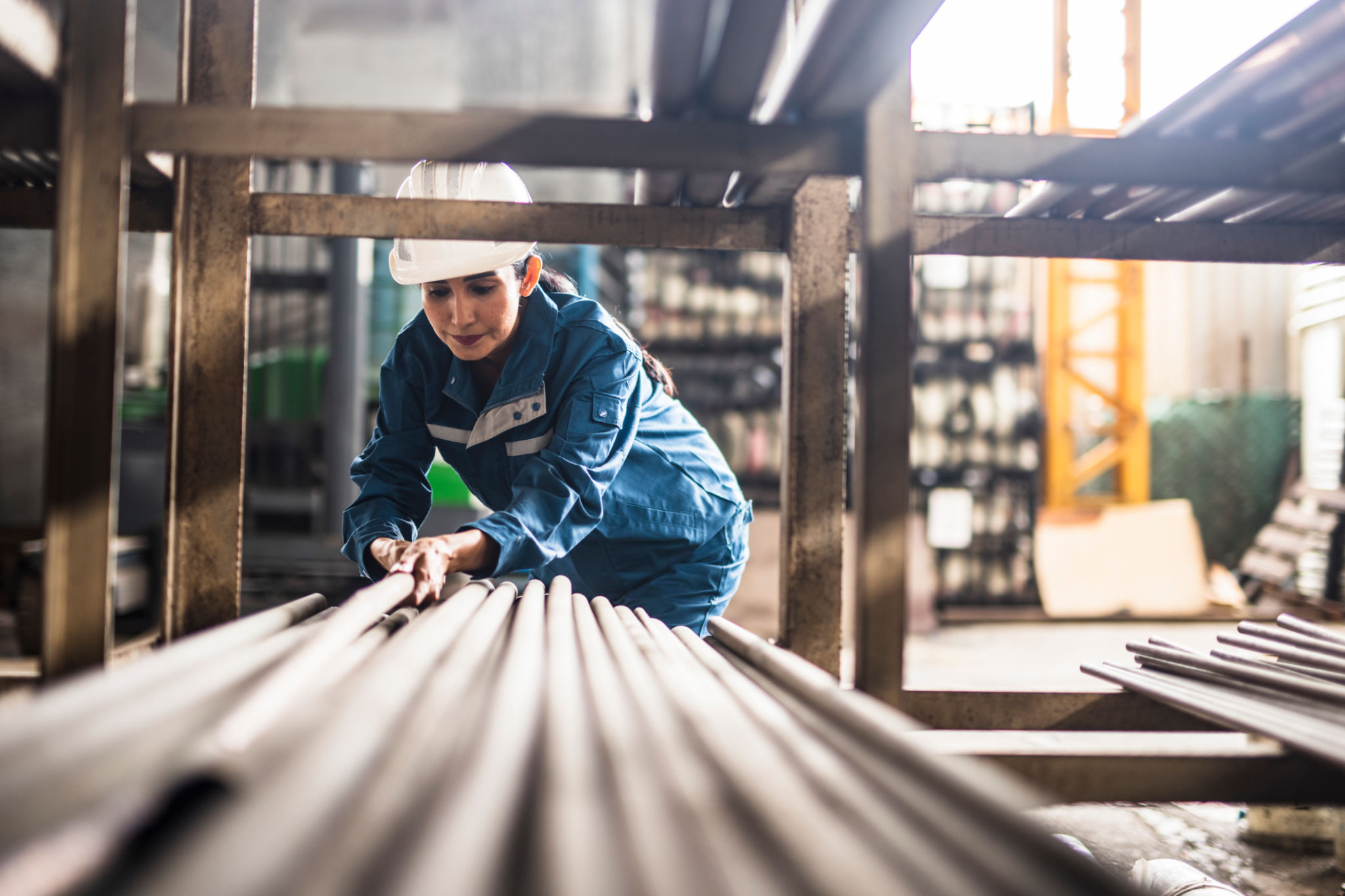
Employee Engagement
An integral part of the firm's success was the active involvement of employees in the continuous improvement process. Training programs equipped staff with the necessary tools and knowledge to contribute effectively. This not only enhanced their skills but also fostered a sense of ownership and commitment towards the company's goals.
Conclusion
The Ottawa manufacturing firm's journey demonstrates the transformative power of continuous improvement strategies. By addressing challenges head-on and implementing targeted initiatives, they achieved remarkable success. This case study serves as an inspiring example for other manufacturing firms looking to enhance their operations and remain competitive in a rapidly evolving industry.