Case Study: How Lean Six Sigma Transformed an Ottawa Business
Ta
Introduction to Lean Six Sigma
Lean Six Sigma is a powerful methodology that combines the principles of lean manufacturing and Six Sigma to enhance business processes, reduce waste, and improve quality. It has been adopted by numerous organizations worldwide to drive operational excellence and achieve sustainable growth.
In this case study, we delve into how an Ottawa-based business successfully implemented Lean Six Sigma to transform its operations, optimize processes, and enhance customer satisfaction. This transformation not only improved their bottom line but also created a culture of continuous improvement.
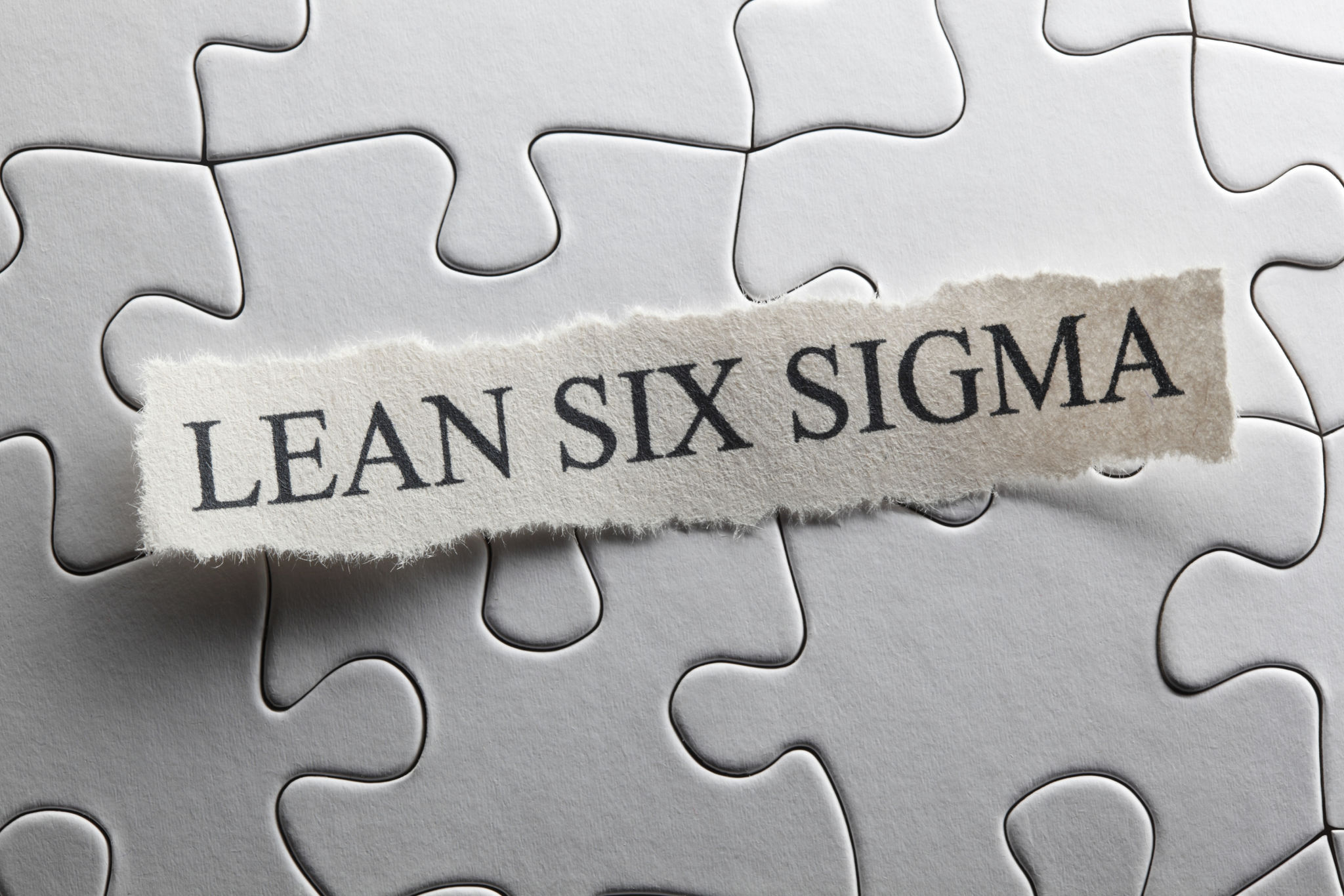
Understanding the Challenges
Prior to implementing Lean Six Sigma, the Ottawa business faced several challenges that hindered its growth. The most pressing issues included inefficiencies in production, high defect rates, and a lack of standardized processes. These challenges resulted in increased costs, customer dissatisfaction, and a competitive disadvantage in the market.
Recognizing the need for change, the management team decided to adopt Lean Six Sigma as a strategic approach to address these issues. This decision marked the beginning of a transformative journey towards operational excellence.
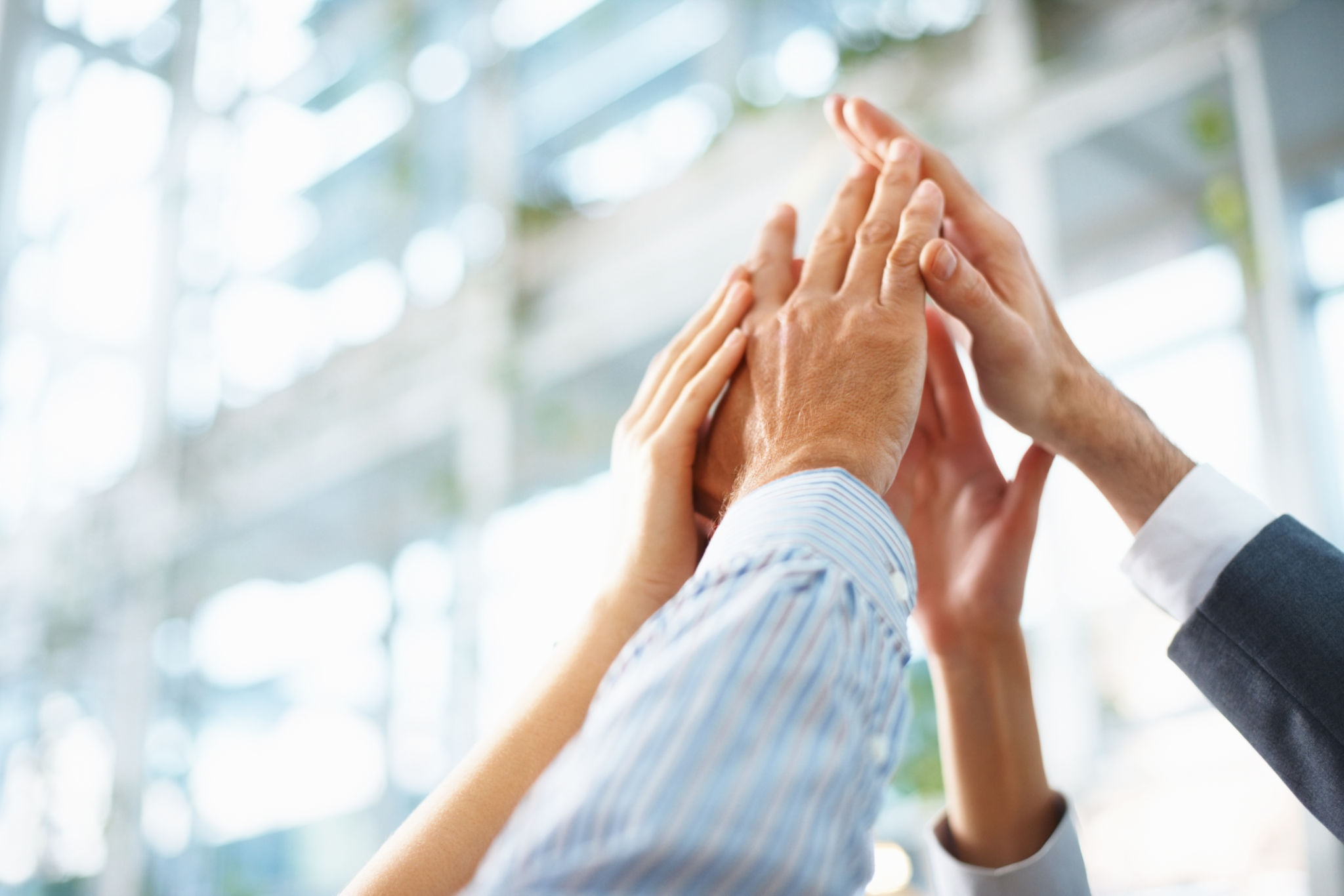
Implementation Strategy
The successful implementation of Lean Six Sigma required a well-structured strategy. The organization began by training key team members in Lean Six Sigma methodologies. This was crucial in ensuring everyone involved understood the principles and tools necessary for effective process improvement.
Next, a series of workshops were conducted to identify critical areas for improvement. Using tools like Value Stream Mapping and Root Cause Analysis, the team was able to pinpoint bottlenecks and determine actionable solutions. This collaborative approach fostered a sense of ownership and commitment among employees.
- Training key personnel in Lean Six Sigma principles
- Conducting workshops to identify improvement areas
- Utilizing tools like Value Stream Mapping

Results and Improvements
The implementation of Lean Six Sigma yielded significant results for the Ottawa business. One of the most notable improvements was a 30% reduction in production cycle time. This efficiency gain not only reduced costs but also allowed the company to meet customer demands more effectively.
Furthermore, the defect rate was reduced by 40%, leading to higher product quality and enhanced customer satisfaction. The standardization of processes also ensured consistency in operations, minimizing variability and improving overall performance.
- 30% reduction in production cycle time
- 40% decrease in defect rate
- Improved product quality and customer satisfaction
Cultural Transformation
The benefits of Lean Six Sigma extended beyond tangible results; it also led to a cultural transformation within the organization. Employees embraced a mindset of continuous improvement, always seeking ways to enhance processes and deliver better value to customers.
Regular feedback sessions and open communication channels ensured that everyone remained aligned with the company's goals. This cultural shift not only empowered employees but also positioned the organization as a leader in its industry.
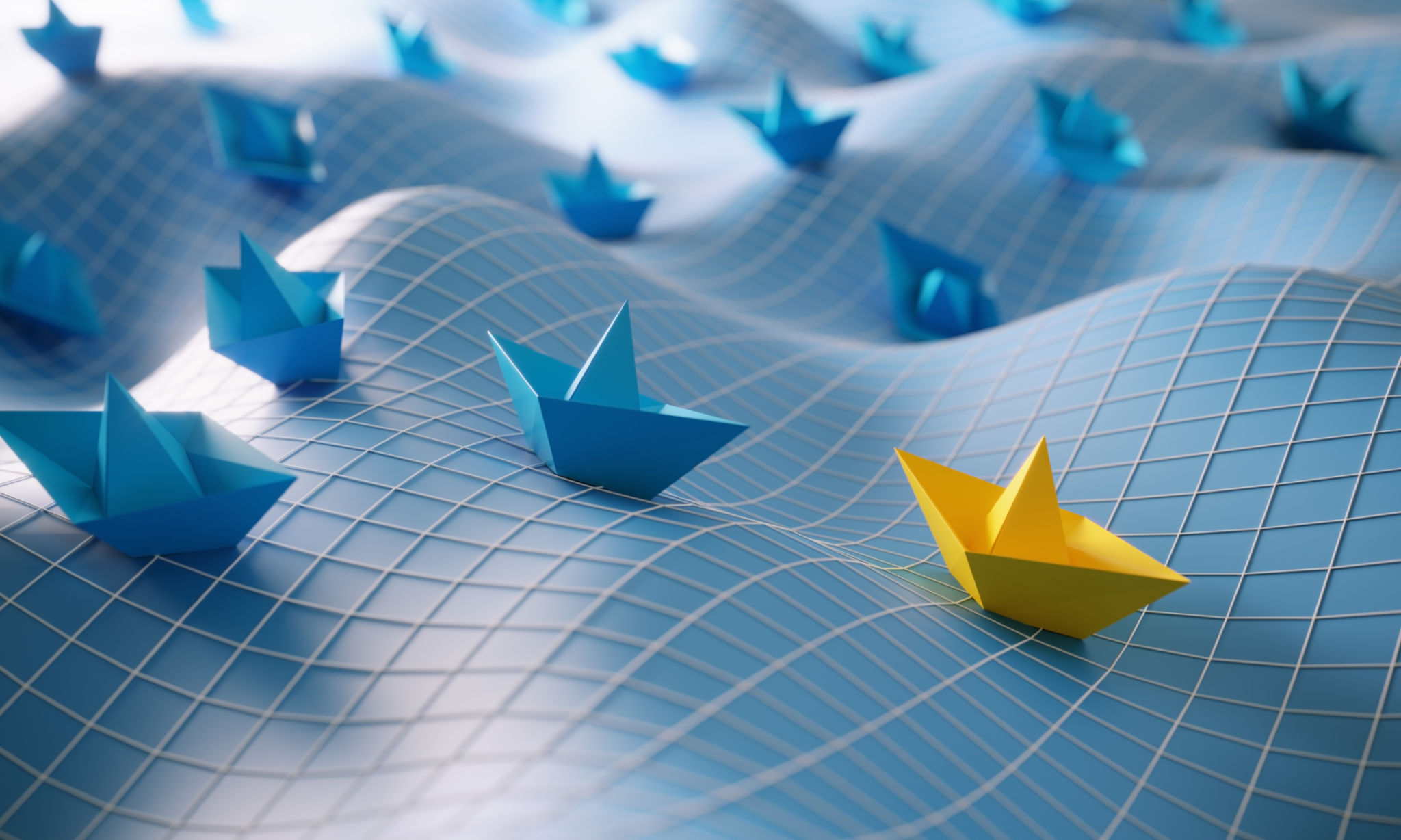
Conclusion
The case study of this Ottawa business demonstrates the transformative power of Lean Six Sigma. By addressing inefficiencies and fostering a culture of continuous improvement, the organization achieved significant operational gains and enhanced its competitive advantage.
This success story serves as an inspiration for other businesses considering Lean Six Sigma as a strategy for growth and excellence. With the right implementation strategy and commitment from all levels of the organization, companies can unlock their full potential and achieve sustainable success.