DIY Process Improvement: Simple Lean Techniques for Small Businesses
Ta
Understanding Lean Techniques
For many small businesses, the concept of process improvement can seem overwhelming. However, with the right approach, it can be quite manageable and beneficial. Lean techniques, originating from the manufacturing sector, focus on minimizing waste and maximizing productivity. The good news is that these techniques can be easily adapted for small businesses across various industries.
Lean techniques emphasize efficiency and value addition, ensuring that every step in your process contributes to the final product or service. By adopting lean methods, small businesses can enhance their operations without the need for major investments.
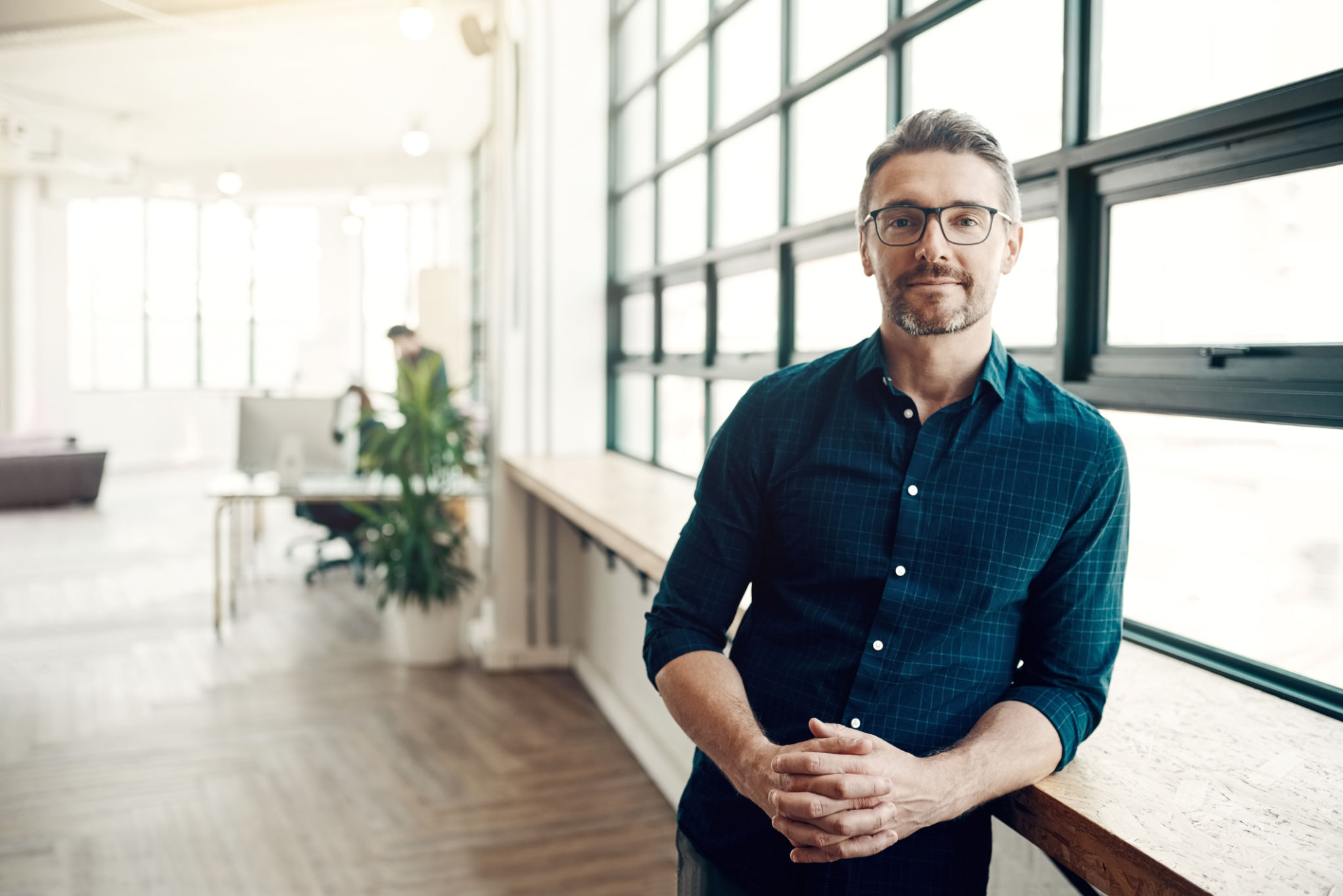
Identifying Waste
The first step in applying lean techniques is identifying waste within your current processes. Waste can take many forms, including time, resources, and effort that do not add value to your business or customer. Common types of waste include overproduction, waiting times, unnecessary transportation, excess inventory, and defects.
Conduct a thorough review of your operations to pinpoint areas of waste. Involve your team in this process, as they can provide valuable insights into daily operations and potential inefficiencies. Once you've identified areas of waste, you can begin to strategize on how to eliminate them.
Mapping Your Processes
Process mapping is a fundamental lean technique that helps visualize your business operations. By creating a detailed map of each step involved in delivering your product or service, you can better understand where waste occurs and where improvements can be made.
Start by listing all steps in a process from beginning to end. Use flowcharts or diagrams to visualize these steps. This visual representation makes it easier to spot redundancies or bottlenecks that slow down your operations.
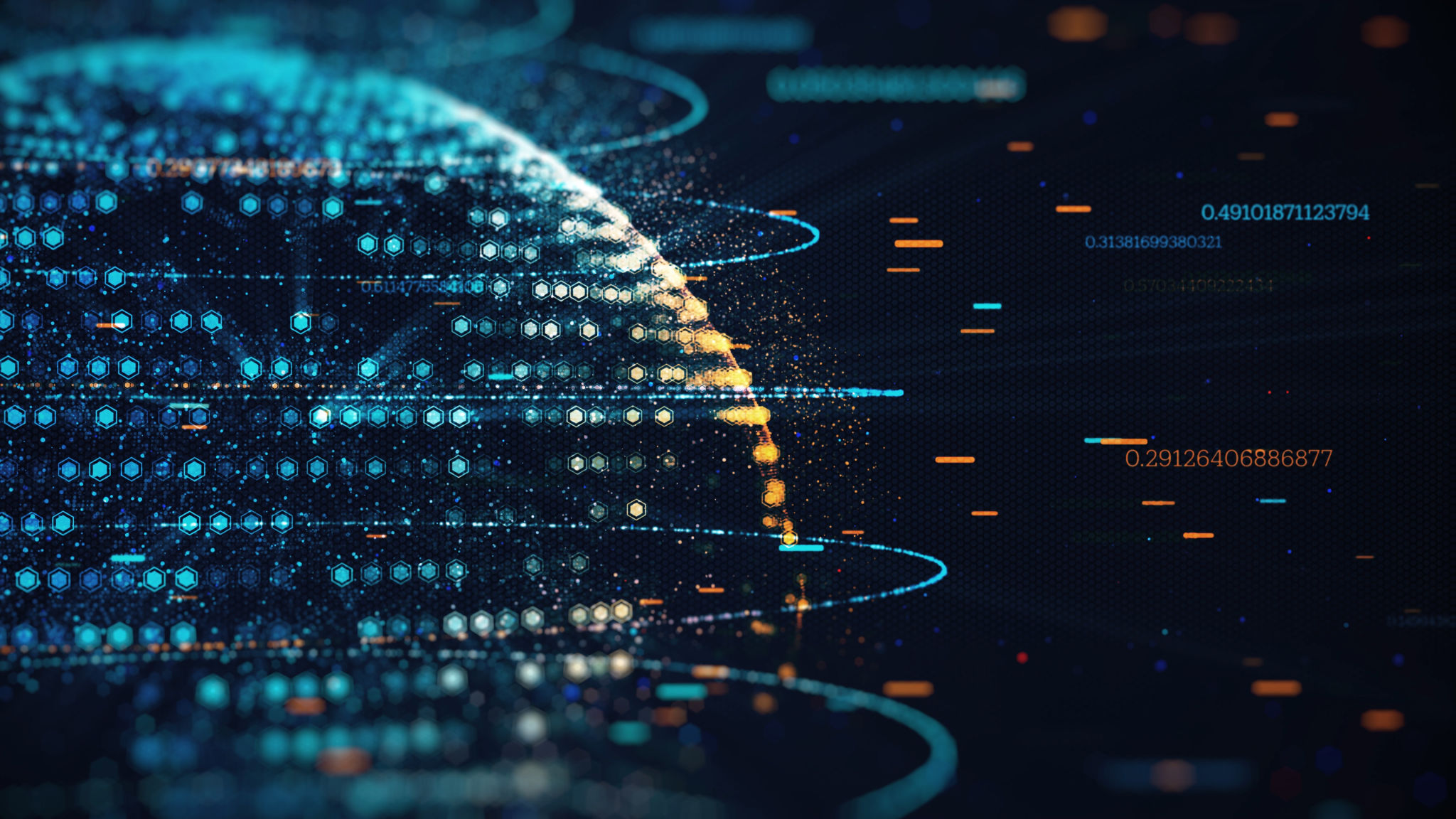
Implementing Continuous Improvement
Continuous improvement is at the heart of lean techniques. Once you've mapped out your processes and identified areas of waste, create a plan for ongoing improvements. This involves setting measurable goals and regularly reviewing performance against these benchmarks.
Encourage a culture of continuous improvement by empowering employees to suggest changes and innovations. Often, those involved in day-to-day operations can offer practical solutions for enhancing efficiency and reducing waste.
Utilizing the 5S System
The 5S system is a simple yet effective lean tool for organizing and streamlining workspaces. It stands for Sort, Set in order, Shine, Standardize, and Sustain. By following these steps, businesses can create a more organized and efficient work environment.
Start by sorting through items in the workspace and removing anything unnecessary. Next, arrange items in an orderly manner to optimize workflow. Regular cleaning (shine) ensures a tidy environment. Standardize procedures to maintain consistency, and sustain efforts by regularly reviewing and refining the process.
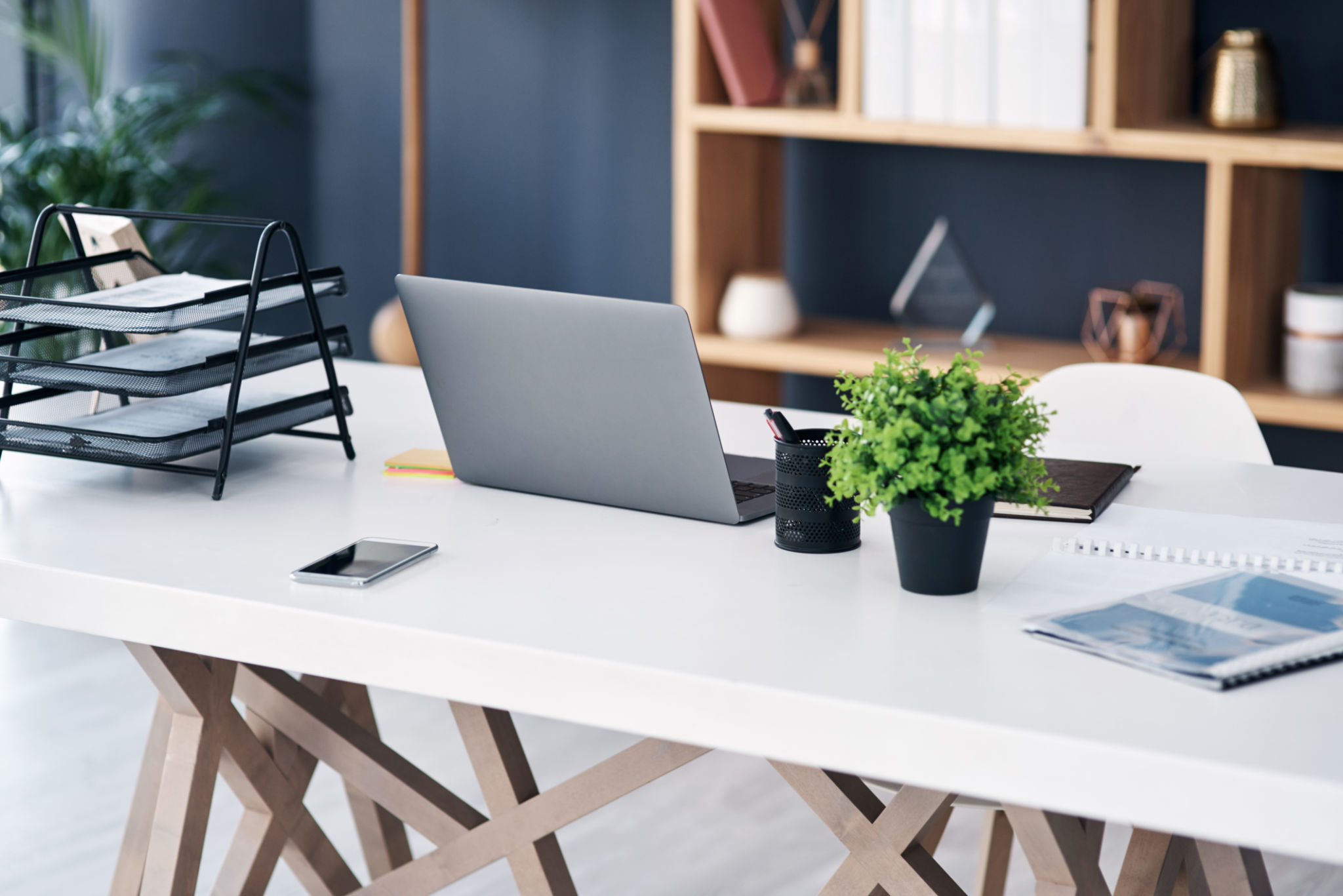
Embracing Technology
Technology plays a crucial role in enhancing lean processes. Small businesses can leverage digital tools to streamline operations, improve communication, and track performance metrics. Software solutions for project management, inventory control, and customer relationship management can significantly boost efficiency.
However, it’s important to choose technology that aligns with your business needs and processes. Avoid overcomplicating your operations with unnecessary tech investments; instead, focus on tools that directly support your lean objectives.
Measuring Success
Finally, measuring the success of your lean initiatives is essential to ensure continuous improvement. Establish key performance indicators (KPIs) that align with your business goals. Regularly analyze these metrics to assess progress and adjust strategies as needed.
By effectively measuring success, small businesses can maintain momentum in their lean journey and achieve long-term improvements in efficiency and productivity.